What’s the difference between non-plated and plated badges?
Protecting your badge: Understanding the difference between electroplated and non-plated finishes for public safety.
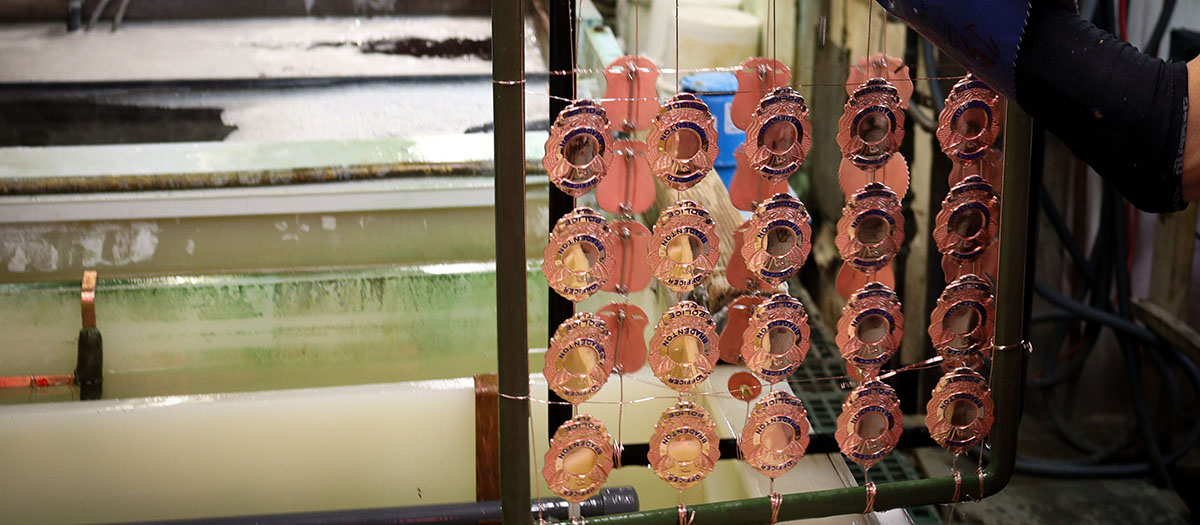
Are you exploring badge finishes and encountering terms like "electroplated" and "non-plated" that might seem unfamiliar? Understanding the difference is important when deciding on a new badge. In this article, we will define “electroplated” and “non-plated” and provide you with some general differences in appearance, cost, and durability.
To start, all high-quality public safety badges are stamped from solid brass. From some of the lower-end suppliers, you might find zinc-alloy and aluminum options, but if you are in the market for a high-quality badge then whether or not the badge is electroplated or non-plated, it will be stamped from solid brass.
Let’s start by defining “what is solid brass?” Brass refers to a range of metal alloys that are primarily comprised of copper. Copper is a reactive metal that oxidizes when it comes in contact with oxygen. When oxidation occurs on the surface of brass the color changes, typically turning brown, green, or darkening, and this is known as “tarnish.” All badges made of brass need to be protected from oxygen so that they do not rapidly tarnish or discolor.
There are two different ways to protect a brass badge. The brass can be either clear-coated or it can be electroplated. In this article, we will explain the difference between badges that are made of solid brass and not plated (non-plated) vs those that are made from solid brass and then electroplated. We will also cover the pros and cons of each.
Electroplated Badges
In simple terms, electroplating is a surface coating process that both protects metal surfaces from corrosion and adds decoration. The process is based on a chemical reaction called hydrolysis and happens when parts are submerged in a “bath.” The process is complex and requires specialized equipment, but when done properly results in a surface finish that is both aesthetically pleasing and durable. Electroplating in the badge industry starts with a nickel coating that is applied over the solid brass. The layer of nickel encapsulates the brass and serves as a protective coating over the brass to keep it from tarnishing.
Nickel is also a decorative layer, but many badges are then coated in either Rhodium or Gold. Gold plating can be applied in different alloys and thicknesses. A high-quality gold electroplate will often include trace amounts of hard metals, such as indium and cobalt to enhance its durability.
Electroplating the badge will completely protect it from tarnish. To further enhance the durability a clear coating can be applied as well. The clear coating will add an additional hard layer to protect the surface from abrasion. A high-quality electroplated finish will not tarnish and will maintain its shine for many years with minimal care required. To learn more about the types of electroplated finishes for a badge, check out our article here.
Non-plated Badges
Non-plated badges are stamped in solid brass and the alloy of the brass determines the color. These badges are not plated but typically will have a lacquer coating applied to the surface to protect a badge from tarnish and abrasion. The quality of the clear coating becomes very important when making a badge without electroplating.
Clear coating quality can vary dramatically so it is very important to understand what is being used. Some are air-cured while others are baked. Baked coatings are superior, but typically require specialized equipment to apply. When evaluating a clear coating you will want to know the pencil hardness and salt spray test results. Pencil hardness measures the surface hardness and the salt spray test measures the corrosion resistance. Generally, a minimum pencil hardness of 6H and a salt spray test of 2,000 hours is a good benchmark.
A non-plated badge has the benefit of being the same color all the way through since the natural brass alloy color is what gives the badge its distinctive color. The surface will oxidize over time and require polishing to maintain luster. To learn more about the different brass alloys and which combinations of copper and zinc, nickel, or tin change a badge’s color, check out our article here.
Which costs more “electroplated” or “non-plated”?
Non-plated badges are generally less expensive to manufacture because they don't require the additional steps of electroplating or the large capital investment in an electroplating facility, but you won't find a significant difference in the market price. In some situations, non-plated badges are being marketed at a premium price through some clever marketing.
Overall, the cost of electroplated vs non-plated badges will be very comparable. The choice of premium plating finishes or brass alloys, respectively, is a more significant cost driver than choosing between a plated or non-plated badge. Aside from your choice of finish or brass alloy, the design of your badge and the manufacturer you choose also factor into the cost.
Does either a plated or non-plated badge hold up better over time?
To give you a quick answer, a high-quality electroplate will do a better job of protecting the badge against corrosion and wear and tear. The plated layer, or layers of metal, adds durability and a good barrier against weather elements. With proper care, it will hold its original shine for a lot longer than a surface that is non-plated.
What does Smith & Warren Recommend?
At Smith & Warren, we produce both electroplated and non-plated finishes, but with few exceptions, our recommendation is electroplated badges for their durability, visual brilliance, and ease of refinishing. While we will consider non-plated badges on a case-by-case basis, we believe plated badges are better suited for daily use in public safety. Hopefully, we provided straightforward answers on the difference between plated and non-plated badges, but as always, if you have any further questions about badges, contact us.
If you maintain your badge, it will last many years. At Smith & Warren, we stand behind our badges with a full lifetime warranty, because we want you to wear our badges for many years. Our dedicated team is here to guide you.